Керамический блок (его так же называют поризованная керамика, теплая керамика, крупноформатный камень, керамический камень, керамоблок) — это искусственный керамический камень сложной формы с пористой структурой. Из него кладут стены, перегородки, перекрытия и ограждения. Керамоблок можно назвать высокотехнологичной заменой пустотелому кирпичу. Так как он позволяет строить «теплые» дома с однослойной стеной.
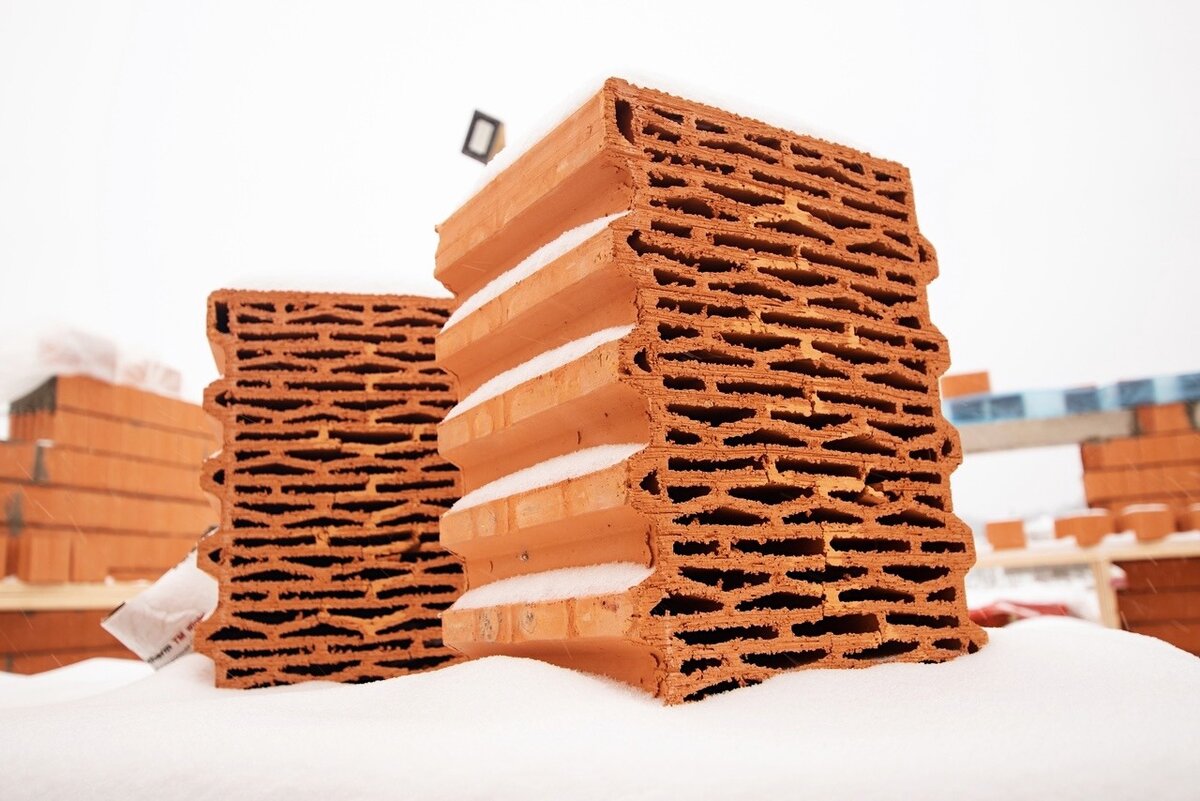
Чем керамоблок отличается от кирпича?
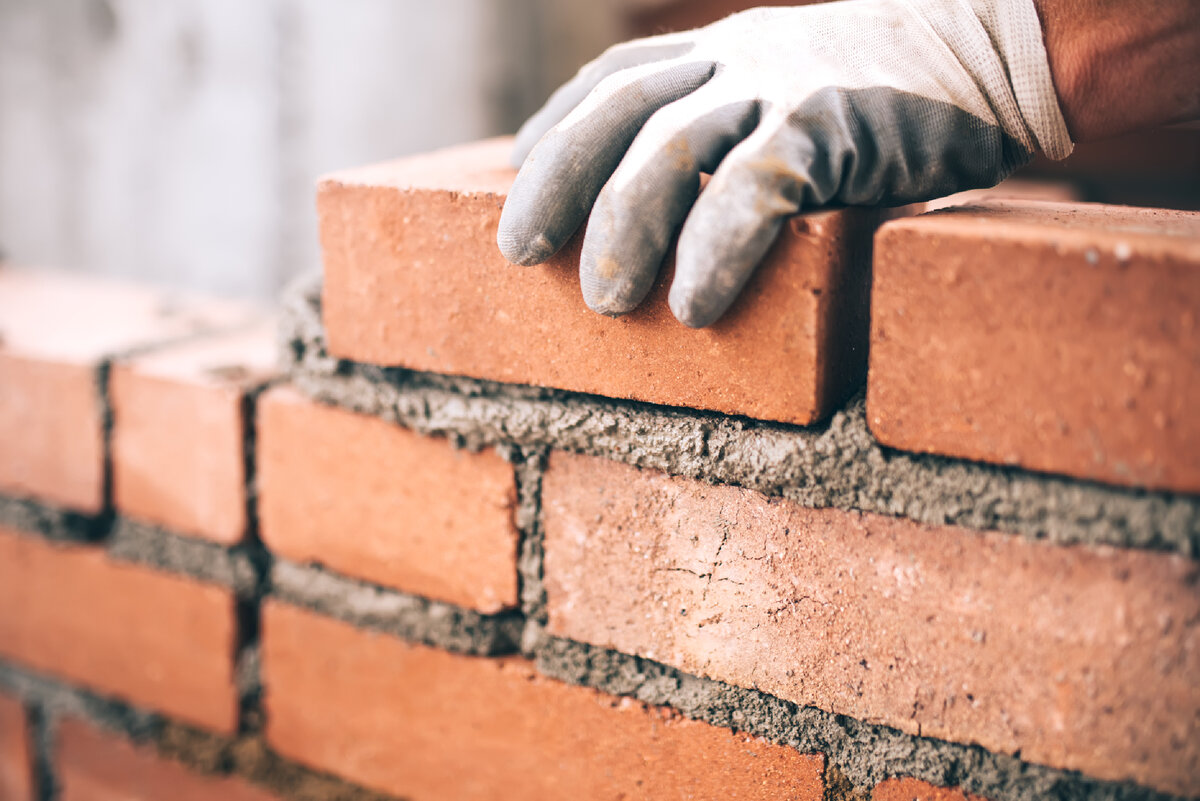
Во-первых, керамоблок в несколько раз больше обычного кирпича: его габариты в промежутке от 250x380x219 до 510x250x219 мм. Размер одного керамического блока в 2,1-14,9 раз превышает стандартный размер кирпича.
Во-вторых, керамический блок имеет очень высокую пустотность: от 50 до 72 %. В то время как у пустотелого кирпича она составляет 25-42 %. Это обуславливает небольшую среднюю плотность изделия — от 650 до 1000 кг/м3.
Во-третьих, керамоблок имеет специальное соединение паз-гребень. За счет этого уменьшается количество мостиков холода и улучшается сцепление между соседними камнями.
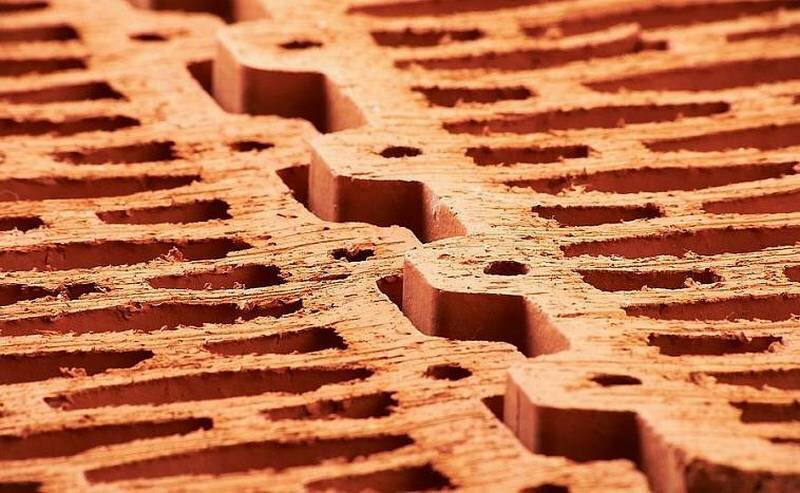
Наконец, рельефная боковая поверхность обеспечивает наилучшее качество сцепления со штукатуркой.
Как изготавливают керамический блок
Производство керамических блоков во многом похоже на производство обычного керамического кирпича. Но при этом оно требует более современного оборудования.
Основной материал для производства — легкоплавкая глина и поризаторы или выгорающие добавки (до 50 % от объёма). Поризаторы нужны для дополнительного снижения плотности изделий и улучшения их теплотехнических характеристик. В качестве поризаторов используют переработанные древесные опилки, солому, торф и другие похожие материалы.
Микс глины и поризатора формирует шихту, которую дополнительно перерабатывают в глинорастирающих машинах. Высокая пустотность изделий требует очень тонких перегородок — 5 мм, а иногда и 3 мм. Поэтому важно раздробить поризатор и каменистые включения в глине до состояния волокон. Из-за этого переработать шихту для керамоблока можно только на современном высокотехнологичном оборудовании.
Из готовой шихты с помощью пресса-экструдера формируются заготовки в виде глиняного бруса. Металлическая струна резчика разрезает его на блоки, которые затем высушиваются от 42 до 72 часов.
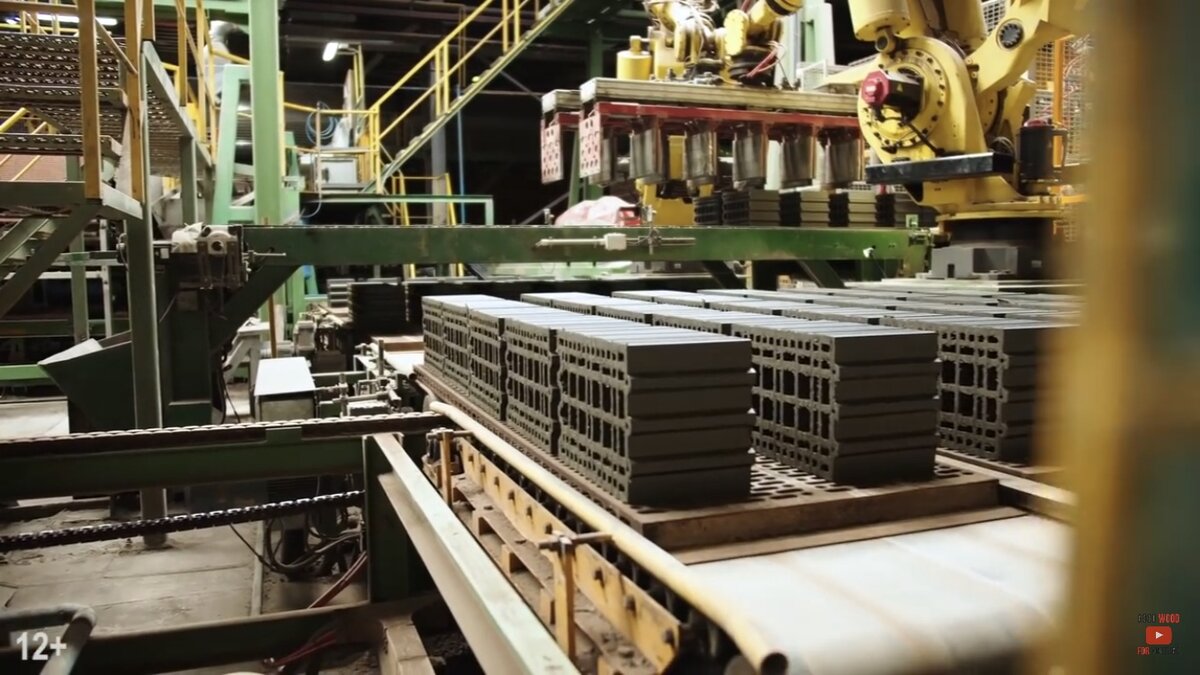
После блоки обжигают в течение 40-50 часов при максимальной температуре от 900 до 1000 °C. При обжиге глина спекается в керамический черепок, а поризующие добавки выгорают, создавая внутри пустоты, которые снижают вес и теплопроводность изделия.
Какие плюсы есть у полнотелого керамического блока?
1. Низкая теплопроводность из-за большого количества пор и пустот;
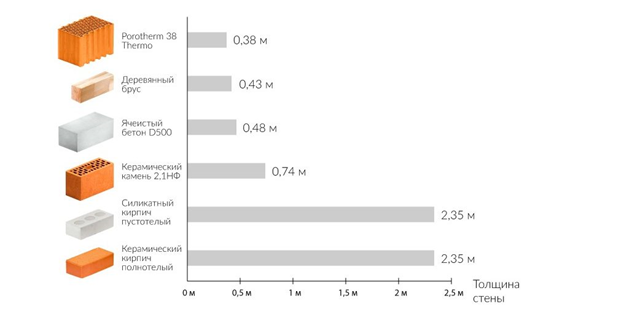
2. Небольшой вес, что снижает нагрузку на фундамент;
3. По сравнению с силикатными стеновыми материалами у керамоблока меньшее водопоглощение. Это гарантирует сохранение теплового сопротивления стены при намокании;
4. Отсутствие деформации под нагрузкой;
5. Высокий уровень звукоизоляции;
6. Ускорение процесса кладки — в 2-5 раз быстрее по сравнению с другими видами блока;
7. Соединение паз-гребень способствует дополнительной прочности кладки;
8. Экологичность;
9. Пожарная безопасность. К тому же при повышении температуры керамика не выделяет вредных для человека веществ.
10. Комфортный микроклимат и сохранность чистовой отделки. Так как керамика, в отличие от бетонов и силикатов, после обжига не содержит влаги.
11. Влаго- и паропроницаемость, что гарантирует отсутствие постоянно влажных от конденсата зон на стене внутри помещения.
Так же отметим, что в отличие от пенобетонных блоков и бетонных блоков с наполнителями, производство керамоблока возможно только на крупных современных заводах. Это снижает риск покупки поддельной продукции со скрытыми дефектами.
Какие есть минусы у керамоблока
- Затраты на доставку от завода до потребителя зачастую выше — так как производство керамоблока выгодно только на крупных предприятиях: от 60 млн штук кирпича в год. За Уралом относительно низкие цены только в Томске за счет короткой логистики.
- Хрупкость керамики. Она требует очень аккуратную транспортировку и погрузку/разгрузку;
- Несопоставимость сверления и штробления с керамоблоком. Для крепления к стене нужно использовать либо химические анкеры, либо специализированный крепеж по пустотелой керамике.
Особенности кладки керамоблока
Первый ряд кладки требует обязательной гидроизоляции и просушки в течение 12 часов. Следующие ряды кладутся через армирующую сетку. Она нужна не для придания прочности, а для того, чтобы клей не попадал в пустоты — это ведет не только к перерасходу клея, но и к снижению теплоизоляционных свойств.
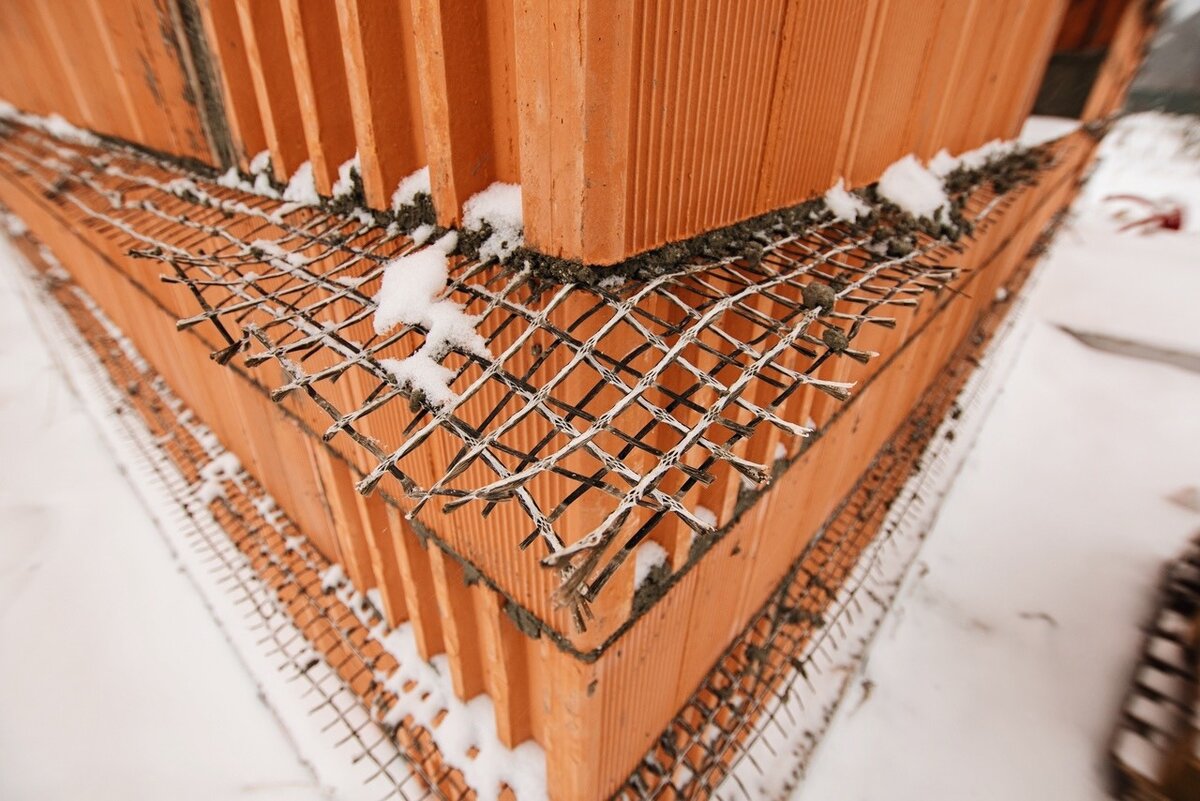
Вертикальные швы соединяются стыковкой паз-гребень — это действительно увеличивает прочность стены.
При наружной облицовке кирпичом обязательна перевязка с кладкой, именно поэтому размеры блока кратны формату кирпича.
Класть керамический блок нужно в сухую погоду при температуре не ниже 5 ºС, а во время осадков укрывать стены пленкой.